浅谈起重机变频器及电气控制系统 变频器是系统优化的关键。可以说变频器的性能基本上决定了起重机变频调速系统的性能。
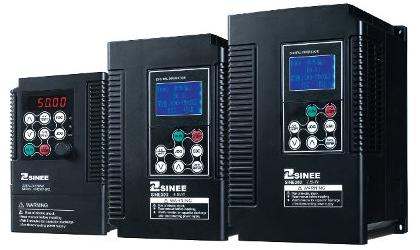
现在起重机的设计者已经可以方便地采用直接转矩控制方式的变频器来控制起重机,这是一种非常适合起重机负载用的变频器。为什么说直接转矩控制(DTC)变频器适合起重机控制,主要有如下几点: (1) 杰出的力矩控制性能。变频器能按照实际负载的大小在小于5ms的时间内提供所需要的输出转矩,负载的转矩直接被控制,由DTC变频器传动的起重机,动态性能优异,能适应冲击载荷,安全性能好。
(2) 突出的速度控制性能。变频器内部的速度观测器可以在没有速度传感器的情况下进行对电动机实际速度的估算,动态的速度误差优于0.4%sec,即使变频器外部速度不闭环控制,电机有足够硬的外特性。
(3) 良好的起动性能。变频器在起动过程中能提供200%额定值的起动转矩,因此起动加速有力,起动非常平稳,并可以在很低的频率下起动电机,有效拓展了实际的调速范围。
直接转矩控制技术是交流传动当今发展的重要成果。变频器在20多年中,已经历了从恒压频比(V/F=C)控制、电压矢量控制、转差频率控制、矢量控制、无速度传感器矢量控制和无速度传感器的直接转矩控制的历程。
大家知道,变频器根据电机的外特性对供电电压、电流和频率进行控制,不同的控制方式所得到的调速性能是不同的。80年代中期,市场上销售的还大都是恒压频比控制的变频器,V/F恒定控制是在控制电机电压变化的同时控制变频器的输出频率,并使二者的比值为一常数,从而使电机的磁通基本保持恒定。这种控制的优点是控制简单,缺点是低速时转矩脉动大,转矩输出性能较差,原因是低频情况下电机的定子电阻引起的电压降所占的比重增大,使得仍按V/F恒定控制已不能使电机的磁通恒定,通常在低于20Hz输出力矩就开始下降,因此低速段电机的力矩往往不足。
为了提高低速段的力矩不得不采取借助提高电压的办法,它所带来的后果是电机被过度激励而导致电机磁路饱和,电机严重发热和效率降低。这种变频器内部对电流是不控制的,无法根据负载实时地改变输出转矩得大小,所以难以满足起重机作业的要求,具体表现在:起动频率必须很高,调速的范围变得很窄,若用于起升机构,动态性能不佳,在要求快速作业或荷重有冲击的情况时电机输出力矩往往不足,容易溜钩,安全性难以保证。
旨在改善V/F恒定控制转矩脉动的问题,各变频器生产商相继开发出电压空间矢量控制(即磁通控制)方式的变频器,方法是对SPWM电压进行修正并加以控制,以获得电机园形磁场,但是这类变频器在低速转矩输出性能方面改善并不明显。
通用变频器真正进入起重机领域是矢量控制型推出之后。矢量控制实现的基本原理是通过测量和控制电机的定子电流矢量,根据磁场定向原理分别对电机产生磁场的电流分量和产生转矩的电流分量进行控制,从而达到控制异步电动机转矩的目的。
矢量控制方式有基于转差频率控制的控制方式、有速度传感器矢量控制方式和无速度传感器的矢量控制方式等。基于转差频率控制的矢量控制方式同样是在V/F=C控制的基础上,通过检测电动机的实际速度,得到相应的控制频率,然后根据希望得到的转矩,分别控制定子电流矢量及两个分量间的相位。这种控制方式的最大特点是可以消除动态过程中转矩电流的波动,从而提高了通用变频器的动态性能。早期的矢量控制的通用变频器基本上都是采用基于转差频率控制的矢量控制方式。
采用矢量控制方式实现精确的磁场定向需要在电动机内安装磁通检测装置,这是一件比较困难的事情;由于矢量控制方式需要准确地输入电动机的参数,还需要使用速度传感器或编码器,甚至需要使用厂商指定的专用电动机,给使用者带来麻烦不说,如果上述条件不满足,就难以达到理想的控制效果。所以矢量控制必须朝无磁通检测器方面发展。人们发现,即使不在异步电动机里面直接安装磁通检测器,仍然可以在变频器内部得到与磁通相应的量,并由此得到所谓的无速度传感器的矢量控制方式。它的基本控制思想是根据输入的电动机铭牌参数,按照转矩计算公式分别对励磁电流(或磁通)和转矩电流进行检测,并通过控制电动机定子绕组上的电压和频率使励磁电流(或磁通)和转矩电流的指令值与检测值达到一致,并输出转矩,从而实现矢量控制。
直接转矩控制也被称为“直接自控制”,这种“直接自控制”的思想是以转矩为中心来进行磁链、转矩的综合控制。和矢量控制不同,直接转矩控制不采用解耦的方式,在算法上不需要进行坐标旋转变换,只要通过检测电机定子电压和电流,借助瞬间空间矢量理论和定子磁场定向的分析方法,直接在定子坐标系下分析电动机的数学模型,计算与控制电机的磁链和转矩,并根据与给定值比较所得到的差值,采用离散的两点式调节器,把转矩值限制在一定的容差范围内,容差的大小由频率调节器来控制,并有此产生PWM脉宽调制信号,去控制逆变器开关状态,实现磁链和转矩的直接控制。直接转矩控制与矢量控制比较,直接转矩控制磁场定向所用的是定子磁链,只要知道定子电阻就可以把它观测出来;而矢量控制磁场定向所用的是转子磁链,观测转子磁链则需要知道电动机的转子电阻和电感。另一个不同之处是直接转矩控制把转矩直接作为被控量,而矢量控制是通过控制电流、磁链等量去间接控制转矩,所以直接转矩控制的物理概念更明确,结构也更简单。
实际应用的效果也证明,直接转矩控制变频器不但性能好,使用也特别方便。不但在起升电动机应用是如此,运用在大小车走行电动机上效果也特别好,因为大小车往往是多电机并联运行由一台变频器供电,直接转矩控制变频器在多电机并联时依然可以DTC控制,充分发挥转矩控制的优点,而矢量控制却做不到这一点。直接转矩控制变频器的种种优点,使得许多起重机生产企业把直接转矩控制变频器作为首选的变频器来加以采用。
2.2 关于起重机控制的专用软件 选用DTC起重机控制的专用软件是一种系统优化的简单办法。起重机应用控制软件往往由变频器制造商提供,该软件针对起重机作业的常规要求而编制,对于一般应用场合是足够了,将这种专用的软件装载到所适配的变频器上,这些变频器将具备如下功能(以ACC变频器为例):
(1) 提供起重机所需要的操作端口。例如起升变频器它通常具有:零位信号检测、制动器延时打开命令、制动器动作应答信号、钢丝绳松弛、提升命令、下降命令、快速停车命令等。
(2) 为提高系统的安全性能,提供了制动器的状态检测、操作手柄的逻辑监控和开机前的力矩校验等。
(3) 在起动之前自动对电机实行直流励磁,油脂浸出设备以保证电动机能迅速地提供输出转矩,并通过调节励磁的时间使电动机的起动与制动器释放的时间相配合。
(4) 为防止出现“倒拉”,软件提供电动机输出力矩记忆功能,每次提升结束都自动地将变频器的输出转矩值记忆下来,当载荷在空中再次提升时,变频器将输出与上一次大小相当的力矩。
(5) 提供电动机功率优化功能,在电机超过同步速进入恒功率区时将自动按荷重的大小限制电机的速度,以保证电机有足够的转矩来控制负载。
(6) 用于下降的斩波制动单元一旦发生异常,电动机将紧急停车。 这种由专用软件控制的变频器给起重机电控系统设计带来莫大的便利,甚至不需要PLC平台就能很好地工作。这种起重机专用变频器构成的调速系统在大吨位,不需要快速地上升、下降切换操作的场合是很适用的。
然而,对于要求快速作业的场合,它的缺点就显露出来了。比如制动器必须在电机实际转速到零时动作,司机会感觉动作拖塌;比如变频器有限的I/O控制端口中有相当的被指定为起重机专用口后,自行组态受到了限制等等。由于变频器内部软件组的开放有一定的权限,一般使用者无力去改变。
为了提高起重机的操纵性能,适用快速作业的要求,较为理想的解决方法是采用ACS标准应用宏的变频器和自行建立PLC控制平台,ACS和ACC这两种变频器在硬件上是完全一样的。设计时可将专用变频器软件的主要设计思想融入到PLC平台中,自行编制控制软件,这样做的优点是束缚少,功能更丰富,控制也更为灵活。例如在控制程序中调用变频器内部第二加减速功能简单方法,可以大大提高整个调速系统起、制动的快速性,也充分利用了变频器的过载能力;例如加入防超速、防溜钩、防倒拉等保护功能,这种系统在铁路集装箱起重机上推广应用,取得很满意的效果。
2.3 关于再生能量的处理方式 起重机变频器在降频过程中,电动机从电动状态自动进入发电状态,电动机由此获得制动转距。减速越快,负载的GD2越大,再生的能量也就越大。处理这部分能量既可防止变频器直流母线电压超过额定电压,造成变频器的损坏,同时又可获得所需要的制动转矩。
起重机在再生能量的处理上,应用最多的是采用外接制动单元和制动电阻的方法,它的优点是将再生能量消耗在电机之外,电动机不发热,适合频繁工作。缺点是这部分再生能量在电阻上以热能形式被白白消耗掉了。这种方式在理论上不及采用可逆变流器的能量回馈型的处理方式好,因为回馈型可以将再生能量回馈电网,使再生能量得到完全的利用。然而,回馈型对以滑触方式受电的起重机是不合适的,任何受电器的跳动都有可能造成逆变的失败,乃至殃及变频器损坏。
对于一个全变频控制的系统,榨油设备采用变频器公共直流母线供电方式是应推崇的方案。起升、大小车、回转所有逆变器连接在一条公用直流母线上,共用一个网侧整流器。此系统中往往有一台或及台工作于再生状态,产生再生能量,这些能量通过直流母线被处于电动状态的其他电动机所吸收,不能完全吸收时,则通过共用的制动电阻消耗掉。这种方式仅管没有回馈电网,但再生能量被得到充分利用。
3 系统的可靠性问题 起重机调速系统的可靠性问题是个很突出的问题。可靠性问题解决得好(实际上也是一个优化的问题),可以充分发挥变频起重机所具有的种种优点,可靠性问题解决得不好,则成为推广变频技术的瓶颈。
3.1 规范设计 起重机变频调速系统的设计规范尚在完善之中,应该看到目前在不少设计中还或多或少地存在不规范的问题,比较突出的问题如:
(1) 电动机设计和选用。对于变频起重机用电动机,大多数以为只要采用变频电机就可以了,其实不然,实际表明沿用过去工频下按起重机起重量以及运行速度来确定电动机容量的方法也许是欠准确的,因为电动机在电网供电下和在变频器供电下的起动电流倍数是差异的,后者约为前者的1/2,因此按上述原则确定的电动机容量在往往显得偏小,起动力矩不足。不仅如此,对电压型通用变频器供电的异步电动机漏抗值应控制在多大为好,未见标准。由于电动机的漏抗与起动电流倍数有关,漏抗大的电动机可以降低谐波,但也降低了起动电流。因此,对于电机的设计、选用有必要引起重视和讨论。
(2) 动力电缆与信号电缆的敷设。这个问题在电气舱和梁上并不突出,可以通过分开敷线来解决。问题集中在有滑动悬挂电缆的场合,鉴于成本考虑,动力电缆与信号电缆混放,设计上不愿意另辟路经。其后果是,信号电缆被干扰,严重时会影响系统正常工作,为此控制系统不得不被动地采取一系列抗干扰措施。变频调速系统如何规范行线,是一个值得在设计中加以研究的问题。
限于篇幅,有关规范设计方面的问题,这里恕不一一例举。但是,大家已经认识到规范设计是保证系统可靠性的第一步,需要我们通过实践去积累经验,加以认识。
3.2 提高设备和器件的可靠性 变频调速系统中,除变频器、可编程控制器外,电动机、电机电缆、机械制动器、主令控制器、制动电阻是较为薄弱的环节。
(1) 电动机。这里讨论电动机的绝缘问题和电动机的发热问题。由于PWM波在传输过程中,电动机和传输电缆的波阻抗不同会引起反射和叠加,400V低压电动机相绕组的首端电压有时可超过1000V。PWM脉冲波的电压上升率约6kV/μs,电动机绕组的电压呈不均匀分布,绕组电压将集中在绕组的首部。所以,绕组的绝缘特别是匝间绝缘应能满足上述电压的要求,试验标准应相应提高。当使用原有绕线式电动机时,必须定期加强绝缘的监测。此外,电动机变频供电与电网供电相比,温升也有所提高,据测试,在相同的试验条件下,电动机在变频器50Hz下的温升约上升5~7度,这种温度升高是谐波损耗所引起的。
(2) 电机电缆。这里主要指起升电动机的电缆。从电磁兼容出发,应采用带屏蔽的园型3+3对称结构的电力电缆,由于市场的需求,实际上国内已经开始生产。但是这种电缆在柔软性方面不及扁电缆,因此往往不被选用。而那种非对称结构以及通常又没有屏蔽层的扁电缆使用后,常常会因电流零序分量大增和产生射频干扰而破坏系统正常工作,这种故障形式往往不确定,给使用和维护都带来了相当的麻烦。所以有必要规范变频起重机电机电缆的使用。
(3) 机械制动器。变频调速拓展了电动机的速度范围,以起升电动机为例,电动机恒功率状态下运行频率可达100Hz,由于运行速度提高,制动器的制动力相应也要提高,采用双制动器设计是合理的,对提高机械制动的可靠性十分有效。
(4) 主令控制器。主令控制器的可靠性直接与制造的工艺、精度和材质有关。在所有器件中主令控制器的故障率差不多是最高的。所以,一个好的控制系统应该有一个质量好的主令控制器,但这往往在设计中被忽视。主令控制器输出的模拟量信号,过去通常采用电位器来实现的,由于电位器安装位置容易走动,磨损问题也比较突出,从提高可靠性出发,更理想的方法是采用档位接点或脉冲编码器通过开关信号转换成模拟信号,转换的方法可以借助PLC的D/A模块。
(5) 制动电阻。制动电阻与制动单元在产生电动机的制动力中发挥重要作用。它的可靠与否,不仅关系到制动性能,还关系到变频器的安全。制动电阻应有高的机械强度,能经受起重机运行产生的振动而不损坏,制动电阻还应具有小的温度系数,否则一旦发热,电阻值迅速增大,制动力矩将明显减小。所以,制动电阻推荐采用不锈钢合金制成的电阻,电阻片之间的连接不能用紧固件而应用氩弧焊进行焊接而成,以确保电阻器物理性能的稳定。
3.3 提高电磁兼容性。 变频器在工作时会产生各种干扰,所以在系统设计时要特别加以注意。电磁兼容对系统优化来说是一个极为重要的标志。提高电磁兼容的做法有:
(1) 在变频器进线侧加交流电抗器。 (2) 采用EMC滤波器。
以上方法可以有效地抑制高次偕波对电网的影响。
(3) 所有进入PLC的开关信号,如限位开关,主令控制器的零位、方向、档位均经过继电器中继,继电器紧挨着PLC安装,由无源的继电器接点与PLC输入口相连,实现无干扰信号传输。
(4) 所有模拟信号采用双绞线或带屏蔽的双绞线传输,双绞线的节距小于10mm,可有效降低传输的噪声。
(5) 电机电缆的屏蔽层应在变频器的PE端良好接地(具体应严格按照变频器使用说明书的规定进行)。内装变频器的电控柜的前后门以及侧板所用的钢板厚度不小于1mm,大面积的通风孔最大直径或对角线尺寸应不大于12mm。柜体应良好接地。
4 信息监控智能化问题 由于变频调速系统系统比较复杂,设备构成众多,加强整个系统的信息监控并朝着智能化方向发展势在必行。
(1) 进行系统状态识别。通过系统的运行参数如电压、电流、运行指令、运动方向、运动速度,输出力矩以及变频器内部信息等,对变频器、制动单元、机械制动器、限位开关、主令控制器、编码器、等关键部位实时进行状态识别。可在司机室安装触摸式显示屏,通过下拉式菜单观测系统的工作情况,一旦工作异常,优先显示故障诊断信息。这样,操作人员和检修人员可以全面及时地了解系统的状态,并可按提示的故障信息去检查和维修,达到准确、快速排除故障的效果。
(2) 加强过程控制功能。提供灵活的I/O配置是处理特殊过程控制的前提,变频器借助PLC或工控机,结合称重系统、位置测量系统实现自动纠偏、电子防摇、自动寻的、自动定位等功能;通过网络通信进而实现整个物流过程的自动控制。 |