探秘地铁列车用制动电阻的优化设计 摘 要:本文通过一种制动电阻的计算及设计实例, 说明了制动电阻的优化设计过程, 并对制动电阻的优化设计方向进行了简要分析。
虽然制动电阻的结构简单、技术成熟可靠,但目前国内外的资料尚没有对各种制动电阻进行总结。因此本文对此进行了归类说明,以便于地铁设计时作为参考。另外,若不对其进行优化设计,设计的制动电阻要么盈余度太大造成投资浪费,要么达不到散热要求导致烧损, 或者因结构设计不合理会导致很多故障的发生。因而,在制动电阻设计时必然要考虑对其进行优化设计。
某制动电阻为一地铁车载强迫通风冷却型制动电阻, 采用车底悬挂方式安装。它包括一台风机, 一个内部装有电阻元件的通风风道及一套监测通风和电阻带温度的监控装置。为了使该制动电阻在满足线路运行条件的前提下达到最优的技术经济效果, 就必须对其进行优化设计。
一、对制动电阻的温升进行优化计算 在计算制动电阻的温升前必须先初步确定该制动电阻的一些基本数据, 如散热面积、冷却方式及风量、规格及重量、风道尺寸等。
1、制动电阻的基本技术参数 制动电阻的基本技术参数如下: 1)电阻段阻值R( 20 8704; 时) 为2. 26 # 2; 2)额定电压为1 800 V; 3)电阻带允许最高温度< 600 8704; ; 4)最大功率为1 120 kW # 2; 5)柜体尺寸(不包括风机及接线盒)为923 mm( 长) # 760 mm( 宽) # 603 mm( 高) ; 6) 制动电阻功率曲线见图1。
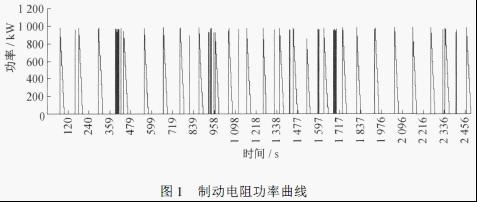
2、制动电阻温度模拟计算 制动电阻内温度场是一个非线性温度场, 要进行精确的模拟分析必须建立相应的有限元模型。但在制动电阻参数设计阶段若参数调整, 又必须重新建立模型, 故有限元模型显然是不适合的。根据对流换热理论, 实际计算时是按以下模型进行计算: 1) 单个电阻元件内电阻带表面温度均匀; 2) 换热方式为强迫对流外掠平板紊流换热。
3、制动电阻温度模拟计算步聚 1) 确定冷却方式: 由于此制动电阻的额定功率较大, 而柜体尺寸很小, 必须采用强迫通风冷却方式。 2) 确定通风截面尺寸: 根据IEC 60322 标准的电阻元件框架对地电气间隙及爬电距离的要求, 计算出电阻元件框架离柜体的最小尺寸; 再由柜体截面尺寸减除该尺寸, 确定出通风截面尺寸W( 宽) #H ( 高) 。 3) 确定风机风量: 根据以往经验, 初步取冷却风速V ( m/ s) , 算出冷却风量为Q( m3 / s)。此参数根据温升计算结果再进一步进行优化调整。
4) 确定电阻带的规格尺寸及质量: 根据通风区域尺寸及电阻值要求, 初步计算出电阻带规格为( 厚) # w ( 宽) # l ( 长) 。 采用强迫对流外掠平板紊流换热模型, 利用VBA 软件, 编制模拟计算程序( 程序界面见图2)输入制动电阻功率曲线, 再分别输入以上各参数数值, 计算出制动电阻各时间点的温度并绘制温度时间曲线。
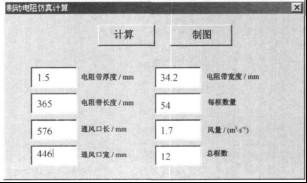
4、模拟计算结果 模拟计算往往不会一次得到理想的结果, 会出现计算温度超出电阻带允许的工作温度; 或者比允许温度低得太多, 造成盈余过大。因此, 需要不断调整计算参数进行反复模拟计算。若计算温度过高,说明散热面积、风量或者电阻带质量不够。这就要相应调整电阻带宽度、电阻带厚度和通风风量, 直至计算温度值接近且低于电阻带允许的工作温度; 反之亦然。
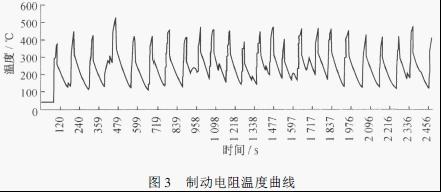
最后确定的参数见图2; 计算出的温度曲线见图3。由图3 可知, 温度曲线最高点为530 , 接近且低于允许的工作温度600 8704; 。考虑到制动电阻内温度场的不均匀性, 此计算结果是合适的。
二、制动电阻结构的优化设计 1、优化制动电阻带的表面形状 优化制动电阻带的表面形状, 合理布置电阻元件, 以强化制动电阻散热能力。前面温升计算采用的是紊流计算公式。但是, 若电阻带表面平直, 电阻带表面的层流底层厚度将明显增厚, 从而使换热系数大大降低。因此必须改变电阻带表面形状(见图4) , 以增加冷却空气的紊流度, 减小层流底层厚度,提高换热系数。
另外, 将相邻两电阻元件的电阻带进行8707; 叉排%( 见图5) , 使气流流经下一电阻元件时的流动方向发生改变, 也有助于提高紊流度, 提高换热效率。
2、防电阻带热变形的结构优化 电阻带的线胀系数为19 # 10- 6 / 8704; , 电阻元件两绝缘子间电阻带长度为365 mm。当电阻带温度由20 8704; 升高到600 8704; 时, 电阻带将膨胀4 mm。如果电阻带两端固定, 产生的弯曲变形将达到23. 5mm。因此, 电阻带两端与绝缘子安装处采用腰形孔, 以保证两端各有2 mm 的调整间隙(见图6) 。除此以外, 在电阻带中部加装一隔离瓷柱(见图7),以保证即使电阻带弯曲变形也不至于引起电阻带间接触短路。
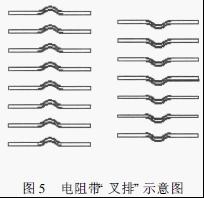
3、优化电阻元件阻值 由于制动电阻由12 个电阻元件组成, 冷却空气经过前面的电阻带加热后温度升高, 从而使靠近出风口方向的电阻带换热系数降低, 使最后面的电阻带表面温度将大大高于最前面的, 从而不能充分利用前面电阻带的热容量。经过计算, 由进风口到出风口分别采用三种阻值为R 1、R2 、R3 (R1 > R 2> R3 )的电阻元件, 提高进风口处电阻元件发热量, 降低出风口处电阻元件发热量, 使各电阻元件的表面温度均匀。
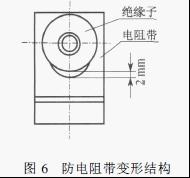
4、制动电阻可维护性的优化 由于制动电阻使用环境恶劣, 不可避免地有烧损现象发生, 并且有大量灰尘需要经常清理, 因此需要使制动电阻的维护方便快捷。本制动电阻将电阻元件设计成抽屉式结构。维护时, 只需将有问题的电阻元件抽出即可更换。另外, 将制动电阻底板设计成锁扣型式, 拉开锁扣即可打开底板对制动电阻内部进行维护作业, 大大缩短了维护作业的时间和强度。
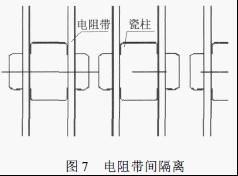
三、制动电阻的优化设计方向 以上只是某一制动电阻的优化设计结果。对于不同线路、不同种类的制动电阻, 其具体的优化设计方法虽有所不同, 但方向都是一致的。即结构尽可能紧凑, 质量尽可能小, 能够承受车辆的振动冲击,能有效地冷却并具有高可靠性和可维护性, 并使制动电阻全寿命周期成本最小化。
为使制动电阻的结构紧凑、质量小, 并能有效地冷却, 就必须对制动电阻温升进行尽可能精确的分析。有条件的可采用有限元分析方法, 使制动电阻带使用量最小化、风量及风道尺寸最小化,并合理布置电阻带, 使温度分布均匀, 避免局部高温的出现。
为能够承受车辆的振动冲击, 就必须使制动电阻具有足够的强度和刚性。通过有限元强度分析和模态分析, 并通过样机的振动冲击试验来验证制动电阻抗振动的冲击性能。为保证制动电阻的高可靠性, 就必须在设计的全过程进行认真细致的失效模式分析, 发现存在的失效隐患并予以改进, 以便有效地避免失效的发生。
缩小制动电阻全寿命周期成本除了选择制动电阻种类外, 还与制动电阻的可靠性、可维护性有很大关系。可靠性不高, 必然故障较多, 维护次数和成本增加; 而若可维护性不好, 必然增加维护的时间和强度, 从而增加维护成本。
四、设计结果验证 通过计算及结构优化设计, 制作了该型制动电阻, 并对其进行了试验验证。由于试验条件限制,不能完全模拟制动电阻功率曲线来进行试验, 因此采用等周期能量模拟试验方法。即试验周期与功率曲线相同, 每个周期输入的能量也与功率曲线每个周期的能量相等。型式试验结果(见图8) 中测点4 的温度曲线为所有测点中检测到的最高温度曲线, 其温度曲线最大值为538。
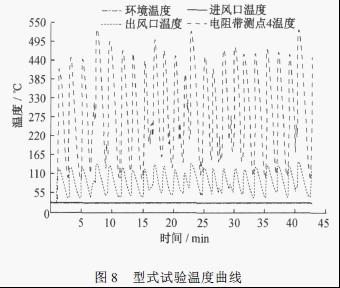
试验结果表明, 模拟计算温度曲线与试验得到的温度曲线基本一致, 基本反映了制动电阻的实际工况。经优化设计的制动电阻获得了国家专利, 并在上海轨道交通1 号线车辆8707; 6 改8%和广州地铁1号线中得到了应用。长期运营的结果表明, 该制动电阻的性能可靠, 维护方便,满足了用户的要求。 |